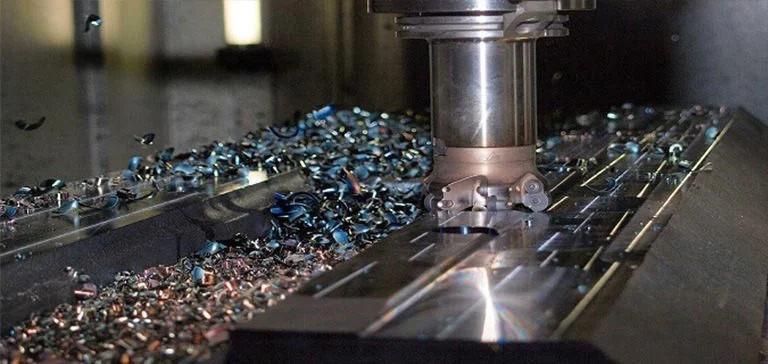
Metal frezeleme aslında hassas mekanik işlemede iş parçalarını kesmek için kullanılan bir yöntemdir. Metal frezeleme genellikle aşağıdakileri içeren iki şekillendirme hareketine sahiptir:
· Kesme hareketi olarak da bilinen ana hareket, dairesel freze bıçağı hareketidir.
· Besleme hareketi olarak da bilinen üç yönde karşılıklı harekettir: dikey, yatay ve dikey. İleri geri hareket, operatöre bağlı olarak ayrı ayrı veya aynı anda gerçekleştirilebilir.
Frezelemenin delme, baralama, kılavuz çekme, raybalama vb. işlemlerde yaygın olarak uygulanan yöntemlerden biri olduğu görülebilir. Geniş uygulanabilirliği ve çok yönlü uygulama teknolojisi ile frezelemenin çok önemli bir rolü vardır.
Freze İşlemenin Avantajları
Yüksek üretkenlik: Frezeleme, hareketleri kullanan mekanik bir işleme yöntemi olduğundan, birçok hareketi birleştirmek ve aynı anda birçok aleti kullanmak mümkündür, böylece ürün işleme süresi kısalır. Ek olarak, freze bıçaklarının birçok kesme gözü vardır, bu nedenle bıçaklar dayanıklıdır, uzun ömürlüdür ve büyük miktarda beslemeye sahiptir.
Yüksek teknoloji: Frezeleme, yüksek teknoloji kullanır, nihai ürünlerle frezeleme yöntemi, toplam işleme ve kesme hacminin yaklaşık %20'sini oluşturur.
Yüksek doğruluk: Yüksek teknoloji kullanımı ve mevcut geliştirilmiş freze makinesi sistemi sayesinde, frezelemenin doğruluğu büyük ölçüde iyileştirilmiştir.
Frezelemenin Dezavantajları
Metal frezeleme yaparken, kesme bıçakları genellikle iş parçasının yüzeyiyle çarpışmak zorunda kalır, bu nedenle malzemede titreşimlere neden olur, bu da iş parçasının kalitesi kadar parçanın doğruluğunu da etkiler.
CNC Frezeleme Nedir?
CNC frezeleme, CNC freze makinelerinde yapılan frezeleme işlemidir. Otomasyon teknolojisi ile CNC freze makineleri, geleneksel mekanik freze makinelerinden daha yüksek ve çeşitli işleme gereksinimlerini karşılayarak, birçok karmaşık parçanın çok yüksek doğrulukla esnek şekilde şekillendirilmesine olanak tanır. CNC frezeleme yöntemi birçok farklı malzemeye uygulanabilir. En yaygın olanları: demir, çelik, paslanmaz çelik, dökme demir, bakır, pirinç, titanyum, alüminyum.
Freze İşleme Yöntemleri
Mekanik frezelemede yaygın olarak kullanılan iki yöntem vardır: ileri frezeleme ve ters frezeleme.
İleri Frezeleme Yöntemi
Freze bıçağının dönüş yönünün tablanın ileri geri yönü ile aynı yönde olduğu bir frezeleme yöntemidir. İleri frezeleme, parçanın yüzey pürüzlülüğünü iyileştirdiği için genellikle finiş frezelemede uygulanır.
İleri frezelemenin avantajları
Kesme derinliğinin kademeli olarak azaltılması ve kayma olmaması nedeniyle yüzey pürüzlülüğü iyileştirilir.
Dayanıklılığın korunmasına ve freze bıçağı ömrünün %50'ye kadar uzatılmasına yardımcı olur.
Kesme kuvveti her zaman parça üzerindedir, bu nedenle şablonları işlemek ve maliyetleri düşürmek daha kolaydır.
İleri frezeleme işlemi nispeten az ısı ürettiğinden ve kademeli olarak azalma eğiliminde olduğundan kesme ısısından daha az etkilenir.
Ters Frezeleme Yöntemi
Freze bıçağının dönüş yönünün tablanın ileri geri hareket yönünün tersi olduğu bir frezeleme yöntemidir. Ters frezeleme genellikle iş parçasının sert yüzey tabakasının çıkarılmasını kolaylaştıran kaba frezelemeye uygulanır.
CNC İşleme Teknolojisinin Avantajları
CNC sürekli gelişen ve hızı artan bir işleme teknolojisidir. Talaşlı imalat yöntemlerine kıyasla birçok olağanüstü avantaja sahip ve mekanik endüstrisinde giderek yaygınlaşan bir şekilde uygulanmaktadır.
1. CNC işleme daha yüksek çalışma güvenliği sağlar
CNC sistemleri tipik olarak, makinelerin çoğunun bulunduğu işleme alanından uzaktaki bir temas masasında çalıştırılır. Bu nedenle, operatörün kesme aleti veya hareketli parçalarla çok az teması vardır, bu nedenle makine kullanıcısının güvenliğini sağlarken, işlemin verimliliğini sağlar.
2. Daha yüksek çalışan CNC işleme verimliliği
CNC makineleri, operatörün makine çalışırken diğer görevleri gerçekleştirmesine izin veren geleneksel işleme kadar dikkat gerektirmez.
3. CNC işleme hurdayı azaltır
CNC teknolojisi, yüksek doğruluk nedeniyle eskisine kıyasla çok daha gelişmiş olduğundan, hurda önemli ölçüde azaltılabilir.
4. Üretim hazırlık süresi azalır
İşleme başlamadan önce, kontrol makineleri için program tasarımı ve kurulumu hazırlamak gerekir. Ancak CNC teknolojisi kullanıldığında süreç daha kısa olacaktır, daha önce gerekli olan birçok aparat ve sıkma aletine ihtiyaç duyulmaz.
5. CNC işlemeyi uygularken hatalar sınırlıdır
CNC programı modern teknikleri uygular, böylece kesim işleminin en küçük ayrıntısına kadar doğru olmasını sağlar.
6. Yüksek hassasiyetli CNC işleme
CNC makinesinin çalışması sırasında üretilen tüm parçaların hatasız ve aynı kalitede olmasını sağlamak mümkündür.
7. Karmaşık işleme işlemlerini gerçekleştirebilir
CNC makineleri, diğer geleneksel işleme yöntemlerine kıyasla çok karmaşık parçaları işleyebilir. Bu şekilde karmaşık işlemleri hızlı ve doğru bir şekilde halletmek mümkündür.
8. Daha düşük takım maliyeti
CNC makineleri genellikle, makinenin çalışması sırasında takım maliyetlerinden yaklaşık %70 tasarruf etmeye yardımcı olan basit sıkıştırma aletleri kullanır.
9. Verimlilik artar
Bir CNC makinesinde işleme, üretkenliği büyük ölçüde artırabilir çünkü CNC sistemi, bir makinenin sistemlerinin tüm parçalarını çok daha kısa kurulum süresiyle daha hızlı ve doğru bir şekilde kontrol eder. CNC sistemleri, geleneksel işleme yöntemlerine kıyasla çok fazla zaman almadan büyük hacimli ürünleri işleyebilir. CNC makinelerinin üretim hızı, hassas işleme süreci sayesinde, birçok zahmetli hazırlık adımı olmadan ve daha mükemmel bir ürün için üretkenliği %80 oranında artırabilir.
10. Depolama ve azaltılmış ayrıntılar
CNC sistemi ürünü verimli bir şekilde yönetebilir, gerekli tüm veri detaylarını saklayabilir. Alt parçalar, bu program kullanılarak aynı hassasiyetle üretilebilir.
İhtiyacınız Olan CNC Makinesine ÖZKA Kalitesiyle Sahip Olun!
Dünyanın en büyük CNC makine üreticilerinin Türkiye temsilcisi olan ÖZKA, sektördeki 40 yıllık deneyimi ve uzman ekibiyle müşterilerine en iyi hizmeti sunmanın gururunu yaşıyor. Metal işleme alanında tüm ihtiyaçlarınıza en uygun çözümleri sunan ÖZKA ile işinizi güvenle büyütün!